We use cookies to give you a better experience on our website. Learn more about how we use cookies and how you can select your preferences.
Oxleigh: Innovative Lithium-Ion Battery Recycling
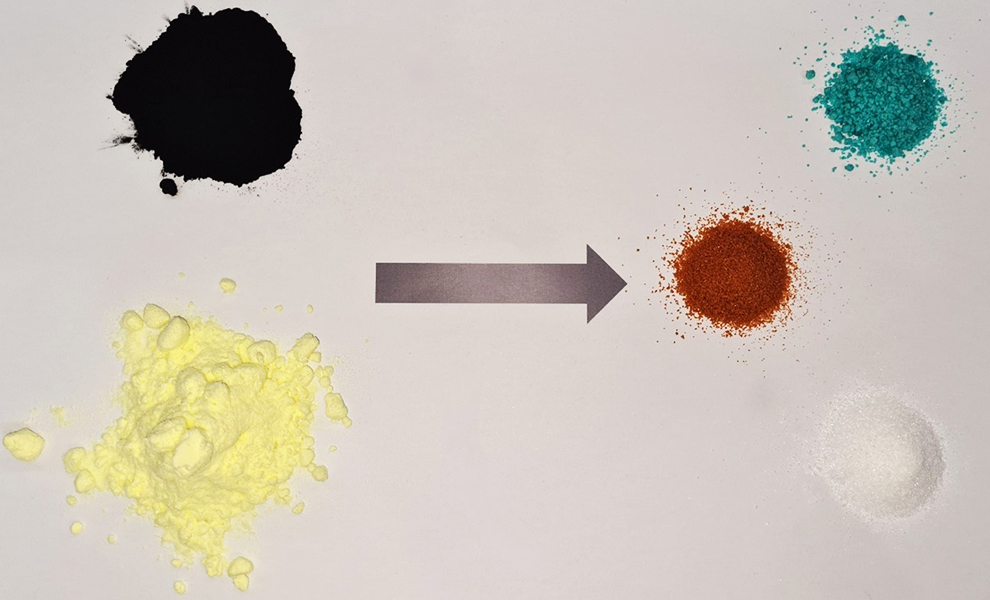
Black mass and sulfur (left) are used to produce valuable metals including nickel, manganese and cobalt (right).
The global demand for electric vehicles (EV) is accelerating rapidly, and with it the demand for lithium-ion batteries. As these batteries reach end-of-life, significant growth opportunities in the recycling space are emerging in Australia and around the world.
In Australia about 39,000 tonnes of EV batteries will reach their end-of-life by as soon as 2030. This is forecast to blow out to 360,000 tonnes by 2040 and to 1.6 million tonnes by 2050, according to the Battery Stewardship Council.
End-of-life batteries are currently disassembled in Australia, and the resulting waste (known as ‘black mass’) exported overseas to process. Pyrometallurgy and hydrometallurgy are the 2 main existing technologies available to recycle the metal containing ‘black mass’ from waste batteries. Both technologies are toxic to the environment, requiring high temperatures and/or large amounts of strong acids. They cannot be feasibly deployed in Australia and many countries.
Bans on the export of ‘black mass’ are increasing in countries around the world. If Australia can’t export our black mass, then the only solution currently is to send it to landfill. This would pose serious, long-term environmental, health, and safety risks.
Chance for localised waste processing
With a $2.75 million Cooperative Research Centres Project (CRC-P) grant, Oxleigh will develop a safe and environmentally sustainable way to recycle lithium-ion batteries locally. To help achieve that, they’re working with:
- University of New South Wales
- Scimita Operations
- Envirostream Australia
- Worley Services.
By targeting this commercial opportunity, our project will foster development of a globally relevant technology in Australia, creating new sovereign advanced manufacturing capabilities.
New technology to use molten sulfur
Oxleigh and its CRC-P partners are developing technology that only uses molten sulfur and air for reaction to process ‘black mass’ from waste batteries. Black mass is comprised of valuable metals such as lithium, nickel, manganese, and cobalt that can be re-used to make new lithium-ion batteries. Oxleigh’s innovative recycling technology has lower capital and operating costs than existing technologies to recycle batteries. It uses minimal energy and will only produce low amounts of waste, with unconsumed sulfur able to be reused in the process.
The technology we are developing is novel as it uses otherwise poorly explored chemistry, reactions between metal oxides and molten sulfur, for a new application - battery recycling.
A pilot plant is being built and operated in the project to supply samples of recycled lithium, nickel, manganese, and cobalt to prospective customers.
With a global shortage of critical minerals to build enough lithium-ion batteries to meet the expected demand, expanded and more efficient battery recycling will ease the reliance on new critical mineral mining developments.
The project supports Australia’s efforts to transition to circular economy and net zero emissions by 2050.
Further information
-
Find out more about the Cooperative Research Centres Projects Grants.
Cooperative Research Centres Projects (CRCP) Grants